As a result of the exponential growth of the world population and the counterproductive effects of their lifestyle on the environment, in addition to natural resources that provide the goods that enable daily life, energy sources are needed to transform and produce said items and conduct everyday activities, such as transportation, cooking, studying, and even entertainment [1]. Many of those activities are possible thanks to the electricity provided by nonrenewable energy sources, e.g. petroleum and coal. However, their depleting availability and the unfathomable cost of the damage they cause to the environment have raised the alarm to humanity regarding the future. As a result, some of the barriers imposed on the development of new technologies to enable sustainable responsible growth have been overcome, mainly their technical-scientific development [2]. This has positively promoted technological innovation and the corresponding emergence of new economical alternatives [3].
The advancement of different technologies focused on clean energy production, including renewable energy sources (RESs). The most common RESs are hydropower, solar power (photovoltaic and thermal), biomass, wind energy and geothermal energy. RESs is one of the most extensively developed scientific fields worldwide because they bring advantages compared to traditional generation systems [4] in terms of low environmental impact. Nonetheless, when comparing cost and efficiency criteria, the cost/kWh in RESs is higher than in conventional energies, which means a current challenge for fostering RESs. International Renewable Energy Agency (IRENA) [5]underlined that the global average cost of all the commercially available renewable energies decreased in 2018 compare to the previous year, and it is projected that by 2019 will continue decreasing thanks to worldwide commercial expansion. The cost of the solar thermal plant decreased 26%, biomass (-14%), onshore solar and wind energy (-13%), hydraulic energy (-11%), offshore geothermal and wind energy (-1%). Regarding efficiency, conventional systems surpass RESs that show variable generation curves such as solar and wind energy, which calls for major studies on RESs in order to compete with conventional systems regarding costs and efficiency.
REN21 [6] proposes a 2019 report, where hydropower is characterized by market stability, rising industry competition and a growing demand for energy storage. The global hydropower market in 2018 looked very similar to the preceding year in terms of capacity growth and concentration of activity. An estimated 20 GW was added to reach a total installed capacity of around 1,132 GW. Pumped storage capacity increased 1.9 GW in 2018, for a year-end total of 160 GW, representing the vast majority of global energy storage capacity. New capacity was installed in China, Austria and the United States. Some new pumped storage projects are being optimized for fast response to changing grid conditions, in part to better accommodate the growing use of variable renewable power technologies.
Pumped-storage hydroelectricity (PSH) is particularly interesting in this field because it can be implemented using currently available technologies [7]; besides, it offers high energy storage capacity and longer discharge [8]. The said storage devices have been intensively used along with intermittent generation systems, such as wind farms (WF), photovoltaics (PV) or both. The use of WF/PSH has been considered in sparsely populated areas [9] because it would stabilize the electricity supply as the plant can be built locally near the wind park, thus storing the surplus energy when demand is low and not affecting the system with intermittent generation. The first implementation of this type of system was carried out in 1984 by the First Hydro Company; it enabled to inject 1728 MW into the grid for 5 hours [10], and it had a remarkable capacity to continue generating electricity for up to 30 years. In the Alpine region of the European Union (EU), 78 PSPSs have been installed. Their power generation and energy storage capacity amount to 32 GW and 14 TWh, respectively [11], and they supply electrical energy to big and small cities in Switzerland, Austria, and Germany, where their energy storage capacity could reach 39 GWh [12]. Dinglin et al. [13] carried out an economic study of 8 MW, concluding that this hybrid system is feasible. Nonetheless, the authors did not consider the peak-valley prices. On the other hand, Reuter et al. [14]developed a model for the economic assessment in Germany and Norway considering the electricity price and the market effects, showing that without substantial public support, the technology is not profitable and will not be adopted for realistic premia. Moreover, Su et al. [15] have put forward a novel integrated transmission mode, which mirrors the actual system operational practices. The total profit of the WF and PSH increased significantly by 5.28% via integrated operation.
Furthermore, Glasnovic et al. [16] have also studied the hybrid generation PV/PSH, concluding that this hybrid system is real, feasible and self-sustaining. The model was tested on the Island of Vis in Croatia, and the results show that it adjusts very well to the characteristics of the subject problem. Additionally, Shabani and Mahmoudimehr [17] conducted a techno-economic assessment of the photovoltaic trackers in a hybrid system PV/PSH, proving its superiority over PV/battery systems. This observation was important because the PSH was nowhere near as expensive as battery storage. Due to their versatility, it can be expanded to parks that integrate these renewable sources WF/PV/PSH. In this regard, Nyeche and Diemuodeke [18] conducted a case study in a coastal community in Koloware, Patani, Nigeria, where they developed a model to determine the economic feasibility of the hybrid plant, using genetic algorithms to optimize PSH. This algorithms minimize the gap between energy offer and demand, concluding that the Levelized Cost of Energy (LCOE) obtained was 0.27 $/kWh, well below the 0.95 $/kWh obtained for diesel powered electricity generators [19]. The integration of pump as turbines (PATs) has increased the flexibility, response time and performance of PHS; however, hybridization of PSH with other storages can increase the range of services and overall system reliability, especially when RESs systems are off-grid [20]. Nonetheless, it has to be considered that PSH has the highest environmental impact as it requires a large scale infrastructure and specific geographic structures [21]. In 2014, the EU had an installed capacity of 100 GW of photovoltaic energy and the same amount of wind energy. In some places, the supply exceeded demand, which forced authorities to define mechanisms to integrate different energy sources by 2050. Specifically, energy storage systems were highlighted as an essential element in any type of strategy in that regard [22]. The worldwide installed capacity of PSH is 120 GW [23], which significantly supports the efforts to integrate PSH and systems powered by wind or solar energy [24]. Among the different storage technologies, pumped-hydro energy storage is the most mature and widely used large-scale energy storage technology.
The main advantages of PATs are low cost of construction and maintenance and high availability of machines and spare parts. The investment cost of PATs can be less than 50% compared to a conventional turbine in scenarios less than 50 kW (pico/micro hydraulic generation). Motwani et al. [25] conducted an annual life cycle cost study (ALCC) for a 3 kw MPH, using a PAT and a Francis turbine with efficiencies of 60% and 80% respectively. For this analysis, they considered the initial cost of the machine (Co), the capital recovery factor (CRF) and annual expenses (Ac). As a result, they found that the cost of the electricity generated per unit between the Francis turbine and the PAT was 6.8 and 5.07, which economically justified the use of PAT for this study. On the other hand, Arriaga [26] presents a viability, design and analysis study of a 2 kW capacity project in the Xiagnabouli province in the Lao People's Democratic Republic for isolated communities (40–500 people). Three energetic alternatives were considered (PAT, V. turbine, PV panels) considering that the total cost was comprised of costs of energy generation equipment (EGEs), civil works (CWs) and energy distribution. The EGE included PAT, induction generator controller (IGC) and related electrical equipment. The CW costs involved the weir, canal, fore bay, penstock and PAT foundation material, excluding the costs for labor and equipment transportation. From the analysis, the lowest installation cost was found in the case of PAT while the PV approach was subject to the highest investment cost. Another important parameter to assess the convenience of energy systems is the levelized cost of electricity (LCOE), defined as the ratio between the sum of all costs over the lifetime of a determined production technology and the total generated electrical energy. Carravetta et al.[27] present a LCOE value of 0.025 €/kWh as a typical value for a PAT installation. On the other hand, the main disadvantages of PATs are the lack of a hydraulic control device, peak efficiency and lower efficiency at part load. Using a pump as turbine generates a loss in efficiency of 3% to 10% for operating under non-designed conditions [28], obtaining lower efficiencies in PATs than in conventional turbines (Pelton, Cross flow), where the pick efficiency was around 80%. The lack of an effective hydraulic control device (adjustable guide vanes, nozzles or runner blades) to match the machine to the available flow or the required performance will result in a relatively fast loss in efficiency in PATs (as well as the hydraulic losses due to flow regulation).
Besides their use in pumped storage power stations (PSPSs), PATs also serve as energy dissipation systems in micro hydropower and as complementary energy storage systems in intermittent technologies [29]. The water in the lower reservoir can be pumped to the upper reservoir during off-peak hours to be stored, thus serving its basic function of storing energy to later generate electricity during peak times. Sivakumar et al.[30] argue that the pumped energy storage systems are more popular even in underdeveloped countries thanks to their operation flexibility when compared to other systems. Nonetheless, other factors such as the availability of appropriate topography and storage capacity must be considered. Venera Jülch [31] presents a detailed analysis on the levelized cost of storage (LCOS) in groups of conventional methods of energy storage:
Pumped-Storage Hydroelectricity (PSH);
Compressed Air Energy Storage (diabatic (dCAES) and adiabatic (aCAES));
Battery technologies (Lithium-ion (Li-ion), Lead (Pb) and vanadium redox flow (VRF) batteries);
Power to gas (PtG) (both hydrogen (H2) storage within a cavern and methane (CH4) storage using the national gas grid).
The author concludes that PSH and CAES are worthwhile for a short-term storage system (100MW power and 400 MWh capacity), while PtG will be more cost efficient for long-term energy storage system (100 MW and 70 GWh capacity).
Nevertheless, different alternatives are currently being implemented and pressure reducing valves (PRVs) stand out among them. PRVs are energy-dissipating elements used in urban hydropower systems to reduce pressure in order to avoid system breakdowns or failures. PRVs are a simple and economical method to reduce pressure, but they are not efficient energy-wise because the energy generated by pressure excess in the tube is not exploited. Different studies maintain that PATs can be a more efficient solution to regulate energy than PRVs [32], [33] because hydraulic turbines enable electricity cogeneration, thus taking advantage of the pressure excess in the hydraulic system. However, factors such as the low energetic potential to be dissipated and the costs associated with implementation make them less attractive as an economically feasible solution, despite the fact that they represent an alternative to control and make the most of the energy in hydraulic systems.
Due to the importance of this topic, this article presents a review of the field and development of PATs for electricity generation in small hydropower plants (SHPs). Its objective is to identify theoretical, numerical, and experimental studies in the literature to analyze the influence of geometric and operating parameters on the performance of PATs.
There are several types of turbomachines whose main function is to take water from a lower to a higher level. Thus, concepts, parts and types of pumps working in inverse mode will be explained (turbines). Besides, selection methods based on the site conditions and a review of the performance predictions will be shown.
Recent studies have evaluated the feasibility of using pumps as turbines. Pugliese et al. investigated vertical-axis pumps running in reverse [34], while Abazariyan et al. determined the effect of viscosity on the performance of the system [35]; in turn, Kramer et al. [36] designed predictive methods to establish the optimal operating point of a pump working as turbine. This is possible because centrifugal pumps are machines that convert the mechanical energy of the shaft into hydraulic energy, thus allowing the working fluid to undergo velocity and pressure conditions according to the requirements of the system. Additionally, these devices are physically and hydraulically similar to Francis turbines, which convert the potential energy stored in water into kinetic energy in the shaft to later produce electrical energy by means of a generator [37]. Pumps can “run backward”, even to the extent of developing a certain momentum if the pressure is sufficiently high as to exceed the starting torque of the impeller and the shaft; for that reason, they can be used to generate electrical energy [38]. Therefore, PATs are pumps that could operate as reaction turbines (similar to Francis and Kaplan turbines) and generate electrical energy if connected to a generator [39].
[Figure 1] illustrates the basic concept of a centrifugal pump, working as a pump and as a turbine. The main components of this hydraulic device are the volute, impeller, and the shaft; they are responsible for generating or receiving the pressures that are necessary to make it work. [Figure 1a] presents the machine working as a pump, where its boundary values are defined by its inlet (suction) and outlet (discharge). As a result, it turns the mechanical energy of the impeller into pressure (head) and kinetic energy (flow). [Figure 1b] shows the difference in flow direction between a radial-flow pump and the pump as turbine. In the latter, the PAT transforms pressure and kinetic energy into mechanical energy applied on the shaft.
Scheme of a centrifugal pump: a) cross-section of the system working as a pump and b) schematic view of the device operating in turbine mode [39]
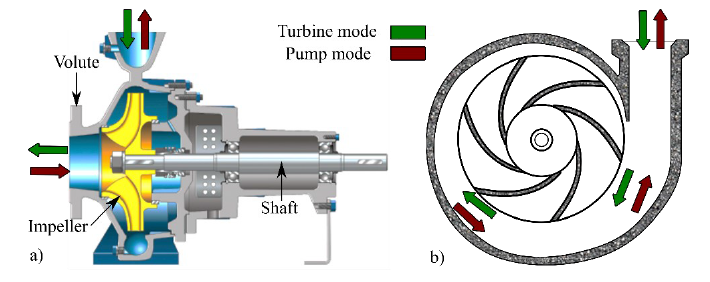
Several types of pumps can be used as PATs; classified according to the orientation of the flow through the impeller, they are generally divided into radial, mixed, and axial flow pumps. Another feature is defined by the geometry of the volute and the number of impellers attached to the shaft; therefore, they are further categorized as single, double, or multi-stage pumps.
The specific speed number, Ns, is a characteristic coefficient derived from the similarity conditions which allow a comparison of impellers of various pump sizes even when their operating data differ. As shown in eq. (1) the definition of the specific speed of the pump is:
(1)
where are: N - the rotational speed (RPM); Q (m3/s)- volumetric flow rate and H (m)- net head, at the best efficiency point (BEP). This equation is used for both the turbine and pump modes of operation.
[Figure 2] presents three types of a single stage centrifugal pumps working as turbines. The relationship between the inlet diameter (D1) and outlet diameter (D2) of a centrifugal pump depends on the specific speed (Ns). Radial-flow pumps are subdivided for high, medium, and low head impellers, and their Ns ranges from 10 to 80, depending on the operating conditions (H). Mixed-flow pumps operate at Ns up to 160, and their axial-flow counterparts do so in a range of Ns from 140 to 400.
Scheme of different types of pumps used as PATs
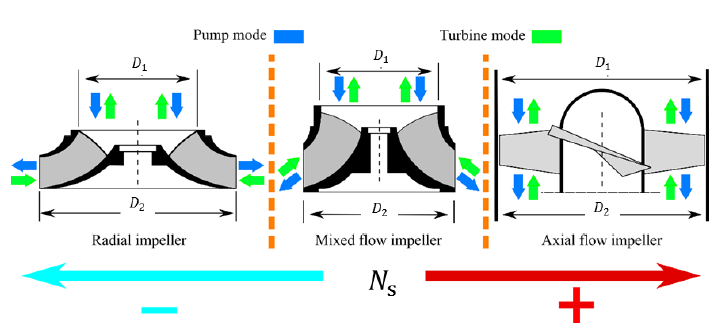
Due to the dynamic similarity of the fluid flow in single stage PATs and Francis turbines, this study is based on the analysis of the latter. Most studies in the literature use PATs that implement single stage centrifugal pumps because of their versatility: they are compatible with a wide range of heads and flow rates and their implementation and acquisition costs are low.
Jain and Patel [Error! Bookmark not defined.] listed different methods to select PATs. They established several selection criteria: available head range, flow range, back pressure at turbine outlet, and desired speed, among others. Nevertheless, they can be reduced to three design criteria: net head (H); volumetric flow rate of the fluid (Q), and hydraulic efficiency (η) of the pump. The head represents the equivalent, in height, of the energy exchanged between the fluid and the impeller. The flow rate describes the volume of the fluid per unit of time that circulates through a section transversal to the flow. In addition, hydraulic efficiency is understood as the relationship between the energy extracted by the PAT represented by shaft power output (P) and the energy available in the fluid (ρgQH), which is calculated using eq. (2), where ρ denotes the density of the fluid and g, the gravitational acceleration [40]:
(2)
An early work that focused on the adequate selection of a PAT as a function of the flow conditions (Q and H) available on site was presented by Chapallaz et al. [41]. They designed a range of application of different PAT types ([Figure 3]) that enables to estimate a range of hydraulic power available at the inlet between 1 and 1000 kW, without considering losses in the system. The sections with an open area—radial, mixed, and axial—are regions where studies are needed to define the full range of action of this type of PATs. Most studies on PATs start at 1 kW of hydraulic power. The shaded regions (multistage radial and double flow pumps) are the most extensively studied types of pump, which are commercially used to generate electricity at pumped-storage plants. This has enabled to completely define (demarcate) the performance area in the guide. In a more recent work, Orchard and Klos [39] proposed more conservative operating ranges for PATs, from 5 kW to 750 kW.
General range of application of different PAT types proposed by Chapallaz, Eichenberg, and Fisher for suitable selection of MHP [41]
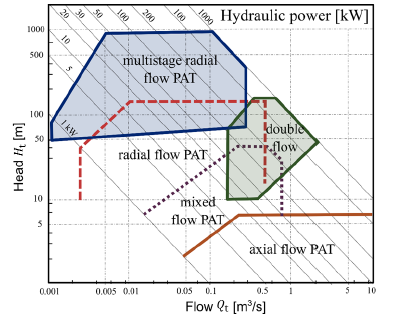
In turn, Kaunda et al. [42] established an alternative method to select a turbine for particular head and flow rate (Q and H) conditions available on site and this process is summarized in the flow chart in [Figure 4]. Besides considering hydraulic parameters to select the PAT, the said method ensures the evaluation of other important factors that can have an impact on the project, such as investment and energy generation costs, the complexity of the design, and the feasibility of the Micro Hydropower Plant (MHP) project.
Turbine selection flow chart for a MHP [42]
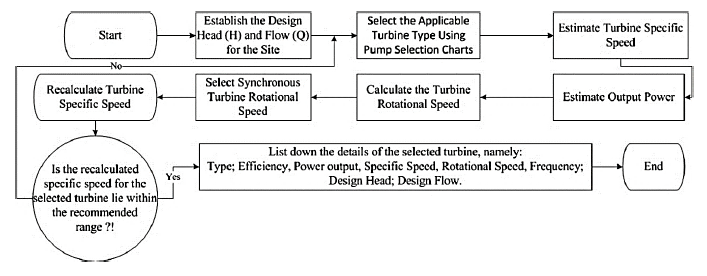
Barbarelli et al. [43] established a methodology for the selection of the PAT applied in MHP by means of a statistical numerical method. This research suggests, first, knowing the hydraulic data of the site where it will be installed regarding head (Hsite) and flow (Qsite); afterwards, the rotational speed (N) of a commercial pump is assumed, in this case 2950 rpm. With the previous data, it is possible to obtain the specific speed of the site, which matches with the specific speed in turbine mode (Nst) as defined in equation 1. Hsite will be equal to HT as Qsite to QT, as showed in [Figure 5]. Several researchers studied the relationship between the BEP in turbine and pump mode, since they differ in terms of H and Q, establishing two conversion factors h (3) and q (4), which depend on the head and flow values at their maximum efficiency point and operation mode (HT,BEP, Hp,BEP, QT,BEP, Qp,BEP).
(3)
(4)
PAT selection procedure - flow chart for a MHP [43]
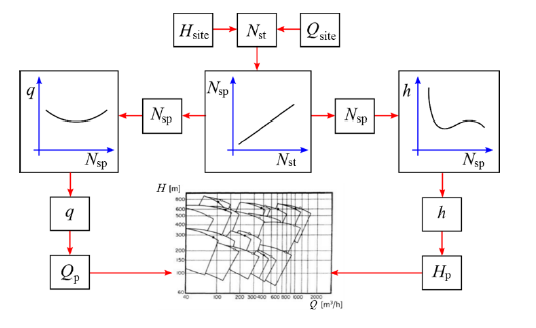
After having Nst, specific speed (Nsp) in pump mode is achieved by means of a linear correlation. There are various methods available in literature to calculate Nsp in terms of Nst. The historical correlation is summarized in Table 1.
Historical development in the Nsp prediction methods of PATs
Year | Name of investigator | Specific speed mode pump (Nsp) estimated correlation | Specific speed mode pump (Nsp)Range | Remarks |
2019 | M. Rossi[44] | 5.0 – 80.0 | 59 review data | |
2018 | S. Barbarelli [43] | 9.0 – 64.0 | 27 hydraulic tests | |
2017 | M. Stefanizzi [45] | 9.0 – 80.0 | 27 review data | |
2016 | X. Tan [46] | 30.7 – 80.0 | 4 hydraulic tests | |
2012 | S.S. Yang [47] | 5.0 – 80.0 | 55 review data | |
2010 | P. Singh [48] | 14.6 – 79.1 | 9 hydraulic tests 4 review data | |
2008 | S. Derakhshan [49] | 14.6 – 55.6 | 4 hydraulic tests 7 review data |
It can be inferred from these correlations that the lowest Nsp range investigated is presented by Derakhshan [49], while the correlation with more experimental validation is presented by Barbarelli [43] with 27 hydraulic tests. Besides, the studies conducted to determine these correlations have used a Nsp lower than 80, meaning that they are radial-flow PAT, which encourages different researchers to explore correlations with axial and mixed PAT to obtain a more comprehensive overview of the single stage PAT types.
There are various methods available in literature to select q and h, based on theoretical and experimental research. The most commonly used methods to obtain coefficients are summarized in Table 2.
Historical development to determine non-dimensional head and flow parameters of PATs
Year | Researcher | Method | Remarks | ||
1957 | Stepanoff [50] | BEP | Accurate for Ns: 40-60 | ||
1962 | Childs [51] | BEP | - | ||
1963 | Hancock [52] | BEP | - | ||
1980 | Grover [53] | Ns | Applied for Ns: 10-50 | ||
1985 | Sharma [54] | BEP | Accurate for Ns: 40-60 | ||
1987 | Lewinsky – Kesslitz [55] | Ns | - | ||
1988 | Schmiedl [56] | BEP | - | ||
1994 | Alatorre – Frenk [57] | BEP | |||
1999 | Sharma [58] | BEP | |||
2011 | Nautiyal [59] | Ns | Accurate for Ns: 18 | ||
2012 | Yang [47] | BEP | Applied for Ns: 5.0 – 80.0 | ||
2017 | Barbarelli [60] | Ns | Applied for Ns: 9.08 – 64.07 | ||
2017 | Stefanizzi [45] | Ns | N/A | Applied for Ns: 9.0 – 80.0 |
Derakhshan et al.[49] and Tan et al. [46] introduced a method based on theoretical analysis to evaluate the BEP. This method is based on the geometrical (Diameter) and hydraulic characteristics of the pump in direct and turbine mode.
Barbarelli et al. [43] proved their methodology thanks to a case study on possible PAT installation in Calabrian water purifier plants of Casali and Sersale (Italy). Depending on the conditions of the site and the design of the system, the Italian government established an incentive for the development of strategies that implement the use of renewable energy equivalent to 0.2 EUR/kWh. This policy results in around 25,000 EUR/year for Casali and 55,000 EUR/year for Sersale, as well as amortization periods under a year. That is a really short time for MHPs and it is an important advantage of this technology.
Because pumps are not working in the mode they were designed for, instabilities in these turbomachines are generated, resulting in efficiency loss, impeller inlet effects and cavitation.
Commonly, studies in this field determine the dynamic response and conduct failure analyses of impellers in PATs. The impeller and the volute can resist static/dynamic pressures they were designed for, reaching up to 20 years of shelf life. Nonetheless, the complexity of the operating features when they are not working as they were designed for creates additional dynamic vibratory behaviour causing instabilities in the system; say a machine designed as a pump working in turbine mode. Fatigue failure may be associated with design problems (geometry, material, and manufacturing processes) and operating conditions that create instabilities in the flow (natural oscillation frequencies-operation) [61]. A particular study focused on the impeller of a PAT that presented a fracture during the operation while undergoing dynamic loads was performed applying the finite element method (FEM). The results of principal stress states and operating frequencies of the PAT in that work are presented in [Figure 6]. In that case, the main causes of the failure were resonance issues due to the proximity between the natural and working frequencies of the impeller and the concentration of stress as a result of the geometry of the connection between the blade and the crown [62].
Failure analysis of the impeller of a PAT: a) Broken impeller and start point of the crack; b) FEM results and distribution of equivalent stress [62]
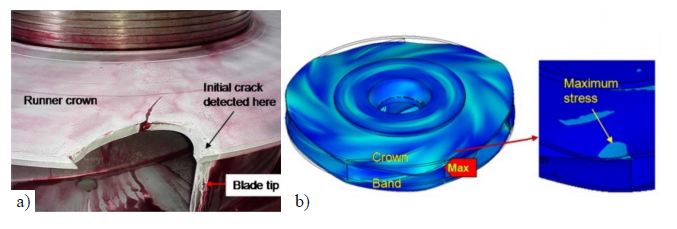
Later, the same authors carried out a numerical (FEM) and experimental (EMA) study with the aim of determining the incidence of the impeller on the dynamic effects that take place inside the PAT. Their results correlate the configuration of the impeller and the failures the impeller presented, as well as the frequencies the impeller underwent and the damages caused by said frequencies [63].
S-shaped characteristics are graphs that enable to identify fluctuations in the performance of PATs. Such fluctuations are associated with transient processes, such as difficulties to synchronize with the electrical components of the turbine, pipe rupture due to excessive pressure, and load rejections, among others. [Figure 7] is a performance curve of flow rate (ԚT) against efficiency (ηT) for PATs, known as S-shaped characteristic. This curve describes the conditions of stable behavior using a dotted line and the unstable performance with a solid line; the interception of the two defines the operating point of the PAT [64].
S-shaped characteristic curves of the PAT [65]
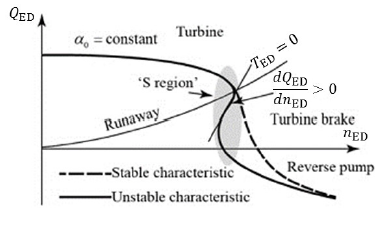
The main reason behind the unstable operation of PATs is pressure fluctuation. Misaligned guide vanes (MGVs) are a widely used method because they improve the S-shaped characteristic of PATs [66].
Different authors have investigated the behavior of PATs in the S-region by means of CFD simulations and assuming a stationary control volume. Liu et al. [67] carried out a numerical study into the S-shaped characteristic, and their volume control was composed of the spiral casing, stay vanes, guide vanes, impeller, and draft tube, using CFX12.1 with the SST turbulence model. Remarkably, they determined that the fluctuations generated by the instability can be mitigated using different misaligned guide vanes. Olimstad et al. [68] conducted an experimental-theoretical study and performed measurements adopting two different methods, transient sampling and throttling valves, to calculate the instabilities of the system. Both methods enabled to measure the S-shaped characteristic curves, and similar behavior was found. However, the transient method as input presented a significant standard deviation of the non-dimensional velocity at two operating points. Regarding the method with throttling valves, the authors recommend using low flow rates only because the head is drastically reduced.
Subsequently, Deyou et al. [69] carried out a numerical-experimental analysis of a 750-kW PAT based on the volume control implemented by D. M. Liu et al. in their study [67] and varied, in the numeric method, the SST turbulence model and the convergence criterion RMSmax< 10−6. This turbulence model resulted in an error below 5% compared to experimental tests, which enables to establish the validity of the numerical model they developed. Such study identified different types of vortices when the PAT enters the “S-region”. In turn, Hasmatuchi et al. [70] take the PAT to this region by experimental means because the PAT is subjected to conditions that were not considered in the design. As a result, they identified the operating conditions of the S-shaped characteristic and obtained models for different PAT prototypes, which provide static and dynamic stability criteria based on CFD simulation and its corresponding experimental validation.
Cavitation may occur in different regions of the pump when local pressure falls below the vapor pressure that corresponds to fluid temperature [71]. Turbines are prone to cavitation, mainly Francis turbines, in a very narrow range of operating conditions. In turbine mode, PATs operate similarly to Francis turbines, which may accelerate the cavitation process compared to the pump mode. Studies conducted thus far adopt two different approaches to cavitation: barotropic and bubble dynamic models. The former defines the density of the mixture based on local pressure, while the latter considers the Rayleigh–Plesse equation which governs the dynamics of a spherical bubble. These numerical models allow to predict cavitation phenomena at different operating points.
Tao et al. [72] designed a numerical-experimental model of a PAT operating as a pump. Their study highlights the measurement instruments that are necessary to capture all the cavitation effects generated by the instabilities of the system, as can be observed from [Figure 8a]. Additionally, they analyzed the way the conditions of the flow rate can cause material to be removed from the blades of the PAT. These results were experimentally validated using the measurements obtained by the equipment under different flow rate conditions and numerically evaluated by means of CFD simulations. Their study leads to conclude that cavitation areas can be predicted based on operating conditions. A later study by the same authors delved into the effect of the flow rate and its angle of incidence with respect to the blades, analyzing the velocity triangles and the formation of the associated cavitation ([Figure 8b]) [73]. Besides, Ješe and Antheaume [74] presented a similar work whose results are included in [Figure 7c], where the study variable is the net positive suction head (NSPH) and its influence on cavitation inception.
Test rig and experimental setup to measure cavitation inception [72]–[74]
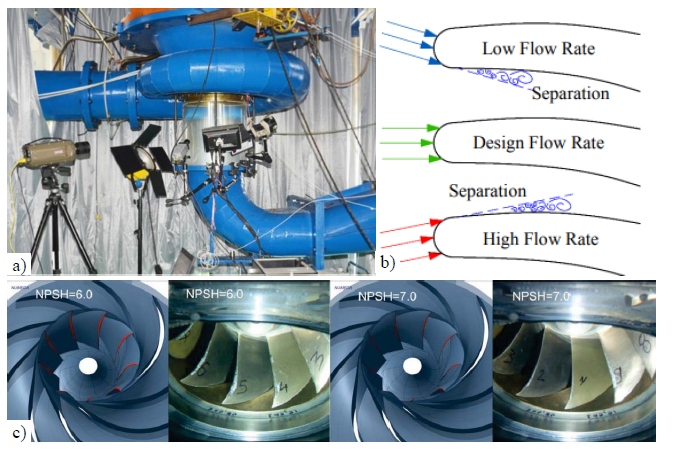
Jintao et al. [75] evaluated the cavitation generated by an impeller of the PAT, which enabled them to compare different numerical models, such as those of mixed-flow and single stage pumps. Moreover, they were able to experimentally demonstrate that the mixed-flow model was better adapted (with an error of 5.5%), while the single stage pump reached 6.3% after its numerical method was validated.
An important part of the state of the art of PATs is focused on increasing the BEP, followed by operating and geometric parameters, which are applied to radial PATs because their impellers are similar to a Francis turbine.
The efficiency of PATs depends on the control of the inlet flow. However, pumps are not usually equipped with such control systems. This aspect is at the core of different studies in the field and, in that spirit, experiments have been implemented on guide blades to control the flow and evaluate the BEP of PATs in turbine mode. Giosio et al. [76] achieved an efficiency of 79%, thus reaching the same efficiency as the device in pump mode. Conversely, Sarasúa et al. [77] studied the dynamic response of PATs in SHPs and analyzed their turbine mode in depth. They analyzed two adjustment criteria to control the load by means of an automatic proportional integral (PI) control system. The first one employs the root locus analysis of the plant dynamic model, which considers the detailed effects of elasticity by means of a continuous wave model. The second one is based on a Pareto approach that finds compromise solutions between the number of oscillations and the absolute median error of the controlled variable. The two criteria are compared with the standard analog controller to optimize the generation process. This may result in an extension of the life of the plant.
Martin Polák [78] described the influence of the change of hydropower potential on PAT operation and compared the experimental results with the model of theory of physical similarity ([Figure 9a]). The model used did not include a change in efficiency similar to models of other authors who also did not consider varying efficiency. However, the results of the experimental verification proved that neglecting the variability of efficiency leads to an incorrect setting of the optimum operational parameters. This applies particularly to the flow rate and the total head dependence on shaft speed, which are the most important relationships when optimizing PAT operation. Frosina et al. [79] used three pumps of Ns 37.6, 20.5 and 64. The experiments have been performed only in steady-state conditions, varying the water flow rate and the pressure at the inlet of the pump, for different shaft speeds. In particular, the flow rate has been varied between 8 and 21 L/s, and the shaft speed between 300 and 2200 rpm. On the other hand, Ismail et al. [80] acquired the efficiency of the PAT, varying the rotational speed (N) between 800 and 1400 [rev/min] obtaining a maximum efficiency of 65.04 at 1100 [rev/min]. The experimental hydraulic system used is shown in the [Figure 9a], [b].
Experimental setup to determine the operating conditions: a) Courses of efficiency in modes 1-6 highlighting the optimum BEP [78]; b) Hydraulic test rig brake system and data logger; c) schematic diagram of the PAT rig [80]
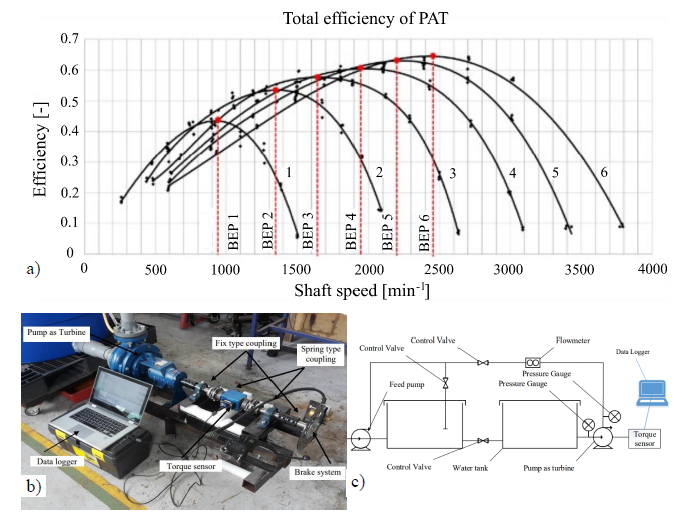
Multi-objective optimization is a mathematical method that allows one to find the optimum value of a mathematical objective equation. Zhu et al. [81] used the criteria of multi-objective optimization in order to determine the incidence of geometrical parameters as blade loading, the blade lean at the high-pressure side of the impeller, and the meridional channel shape on the impeller performance. They started with reverse engineering to obtain a geometric model of the impeller and CFD simulations to estimate the objective functions and the validation of the optimization results. Subsequently, they developed a design of experiments (DOE) that determined the distribution of the sampling points in the design space. Using the root mean square (RMS), they also correlated the design parameters to the required parameters. As a result, the computational cost was significantly reduced and a PAT impeller with high BEP and operating stability was obtained.
The improvement of the performance of PATs equipped with a radial impeller has been addressed in many studies. The latter aim at determining the geometric effect of the impeller–volute assembly on the BEP of this turbomachinery. Table 3 classifies and summarizes different studies, the implemented method, where the applied methods were classified at 3 different cases; the first one is Theoretical (T), next one is Numerical (N) and the last one is Experimental (E). These geometric changes were made, such as impeller diameter (A), inlet impeller rounding (B), number of blades (C), splitter blade (D), blade wrap angle (E), blade profile (F), blade thickness (G), blade lean (H), and blade inlet angle (I).
Summary of different geometric modifications to evaluate the performance of PATs
Ref. | Geometric | Method | Change in BEP | Remarks | |||
Parameter | T | N | E | ||||
Yang et al. [82] | A | X | X | ↓ 2.97% to 4.11%, | Efficiency study in pump and PAT mode. The diameters of the impeller trimming to 92.16% ↑ 1.93% (in pump mode) and 84.31% ↓ 1.6% (in PAT mode) with respect to the original dimensions. | ||
Jain et al. [83] | A, B | X | A = ↓ 3.79% to 11.04% B = ↑ 3.00% to 4.00% | The diameter of the impeller was reduced to 10% and 20% of the original (250 mm). Besides, the inlet of the blade was rounded, and its radius is equal to half of the thickness of the blade. These two design parameters were evaluated at different rotational velocities. An empirical correlation was developed for efficiency at the BEP(nBEP) by regression analysis of the experimental data based on blade rounded impeller. | |||
Wang et al. [84] | A | X | X | ↑ 1.73% to 3.32% | Efficiency study in PAT mode cutting the diameters of the impeller in 96.08% and 92.16% of the original. | ||
Singh and Nestmann [85] | B | X | X | ↑ 1.00% to 2.00% | A theoretical model based on turbomachine fundamentals was developed with the help of a zonal approach in a PAT control to identify the internal variables and their behavior. Experimental study of the effects of impeller rounding in a wide range of PAT shapes to accurately characterize these effects with respect to internal hydraulic variables over the complete operating region of the PAT (part-load, BEP, and overload). | ||
Ismail et al. [86] | B | X | ↓↑ -1.03% to 0.18% | Simulation results were compared with the manufacturer’s data sheet to validate the accuracy of the simulation model. | |||
Doshi et al. [87] | B | X | X | ↑ 0.50 to 2.50% | Interpretation of the quantitative flow effects of three individual modifications of blade rounding viz inner shroud rounding, and outer shroud rounding with respect to zones of a PAT control volume. A refined model of internal flow variables linked to the external variable was developed to analyze the effect of several modifications. | ||
Yang et al. [88] | C | X | X | ↑ 0.78 to 1.49% | A numerical analysis of the performance of PATs shows there is an optimal number of blades for a PAT to achieve the highest efficiency. The PAT in that study reached the highest efficiency with eight blades. An analysis of the unsteady pressure values that were obtained indicates that the amplitude of pressure pulsations is reduced as the number of blades increases. | ||
Ismail et al. [89] | C | X | ↓↑ -0.20% to 0.47% | The number of blades was varied to 5, 6, 7, and 8. All the impellers were found to have a similar performance profile. | |||
Sun-Sheng et al.[90] | D | X | X | ↑ 3.42% | This numerical study predicted the performance of an impeller with and without splitter blades. It shows that the PAT’s efficiency increases and its required pressure head decreases when splitter blades are added to the impeller. | ||
Yang et al. [91] | D | X | ↑ 0.78% to 4.04% | An experimental method was developed to determine the effect of the splitter blade´s main geometry on the performance of a PAT, corresponding to the splitter blade circumferential bias degrees, outlet diameter, number of blades and outlet deflection angle. Enhancements respect to standard impeller were reported in this study. | |||
Yang et al. [92] | E | X | X | X | ↑ 0.21% to 0.52% | The flow rate increases at the BEPs, and the amplitude of increase in the flow grows as specific velocity rises. The hydraulic loss distribution analysis shows that the hydraulic loss within the impeller compensates most of the total hydraulic loss, and the ratio to total hydraulic loss grows along with the increasing specific speed. | |
Bai et al.[93] | E | X | X | ↓↑ -2.53% to 2.23% | The blade wrap angle increases with the forward-curved blade impeller, and the flow state of the hydraulic turbine which in areas of a low flow rate improves significantly. Compared to performance curves, the maximum efficiency of the turbine climbs from 64.86% to 67.53% when the blade wrap angle increases from 20° to 65°. However, a change in blade wrap angle from 65° to 80° results in a decline in maximum efficiency from 67.53% to 66.53%. | ||
Du et al.[94] | E | X | X | ↑ 1.35% to 3.1% | The efficiency of the PAT increases from 12.9% to 16.0% by changing the blade wrap angles, and maximum efficiency occurs when the blade wrap angle equals −60°. The lower blade wrap angle may lead to the reduction of hydraulic loss in the impeller; as a result, the total water head loss on the impeller will decrease. | ||
Miao et al. [95] | F | X | X | ↑ 2.91% | The purpose of fluid dynamic optimization of the PAT’s blade profile is to guarantee a better performance when it is running at the BEP. Using the genetic algorithm to carry out the optimization, fitness evaluation should be done for each population. Latin Hypercube experimental design method was used to select as many sample points as possible to train the back propagation (BP) neural network. | ||
Yang et al. [96] | G | X | X | ↓ 0.47% to 1.19% | Blade thickness was increased from 2 mm to 6 mm; the hydraulic loss factor k, by 1.89%, 19.22%, and 30.50% for the low, medium, and high specific speeds of the PATs at the BEP. Flow rate, required pressure head, and generated shaft power are increased, and efficiency is reduced as blade thickness escalates. | ||
Dai et al. [97] | H | X | X | ↑ 0.67% to 1.81% | The efficiency of the PATs by leaning blades declines at most flow rates, with a slight increase at larger flow rates. After a certain inclination of tongue, the efficiency increases over full flow rates. After counter-leaning blade and tongue, the efficiency remains basically the same with conventional PAT. The angle is leaned by 75.5° and 44°, the flow rate at BEP is increased by 10 m3/h and 5 m3/h, respectively. | ||
Yang et al. [98] | C,I | X | X | X | ↑ 4.38% | High efficiency was obtained by using two efficiency geometric methods: the number of buckets and the angle of attack at an impeller with external diameter of 235 mm. | |
Wang et al. [99] | B,I | X | X | ↓↑ -4.72% to 0.68% | Authors conducted a study using a pump with Ns 193 with an angle of attack of 72º and an efficiency of 82.14%. Three different angles were assessed (60°, 90°, 105°), obtaining a maximum efficiency with an angle of 60º and an efficiency of 82.82%. A range of 60º to 90º is recommended for this pump. | ||
Wang et al. [100] | B,I | X | X | X | ↑ 7.93% | The study was conducted using a pump with Ns 18.1 and an angle of attack of 71º and an efficiency of 59.98%. Three angles were assessed (90°, 111°, 135°) with a result of 67.91% | |
Wang et al. [101] | B, I | X | X | X | ↑ 5.45% to 8.07% | Three pumps with Ns of 18.1, 36.4 and 52.8 were used, with an efficiency of 59.98%, 63.75% and 71.86% respectively. A maximum efficiency for the pump with Ns 36.4 was obtained using combined geometric changes such as buckets rounding and angle of attack. |
An important result from the literature review was the finding of nine (9) geometric parameters resulting from the theoretical behavior of the optimization in pump mode, implemented also in turbine mode to analyses its influence in the efficiency of the turbomachine. These 20 researches used theoretical, numerical, and/or experimental methods. [Figure 10] describes the change of efficiency through the geometric modification of the impeller. On the abscissa, there are nine geometric parameters plus the combination of some of them, while on the ordinate, the efficiency variation regarding the original impeller is specified, finding results that increase or decrease according to the implementation of these parameters. Some of these researches resulted in a negative incidence: A, G and in some cases B, C and E. The geometric parameter with the highest incidence is D, with an increase of 4.04%, although this research only considers the numerical analysis method. Other authors use T/N/E methods such as those carried out by [98], [100], [101], which generate higher incidence, since they combine different geometric parameters to obtain favorable conditions with a maximum value of 8.07%.
Incidence of geometric parameters in the efficiency of PATs
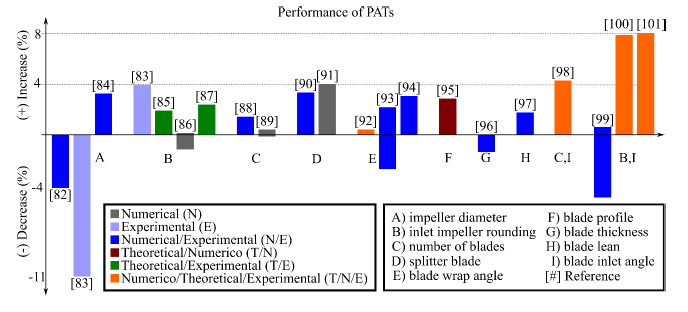
The PATs are simpler devices, low cost, easy acquisition, and maintenance compared to conventional turbines, which represents a feasible solution to the problem of energy supply in non-interconnected areas. Among the different existing centrifugal pumps, the one most used as a turbine corresponds to the simple impeller due to the dynamic similarity with respect to the Francis turbines.
In this review, a summary of the different methods of selecting and predicting the performance of the single stage pump was analyzed. In addition, non-dimensional head-h and flow-q conversion factors were presented to facilitate pump selection. The authors of this review did not find similar information for axial and mixed pumps. For this reason, it is necessary to determine different correlations and conversion factors q and h for these pump types
Theoretical, numerical and experimental studies have been carried out in order to determine the incidence of geometrical and operational parameters in the efficiency of the PATs, which is generally lower compared to other generation technologies, due to the instabilities that occur in the associated fluid. The instabilities are mainly associated with the geometrical configuration of the rotor and the different operation parameters from the design ones. Geometrical parameters of the rotor such as impeller diameter (A), inlet impeller rounding (B), number of blades (C), splitter blade (D), blade wrap angle (E), blade profile (F), blade thickness (G), blade lean (H), and blade inlet angle (I) have been studied by different authors. The geometric parameter with the highest incidence according to the research is that of the intermediate blades (D) with a 4.04% increase in efficiency, but this study considers only numerical analysis. Researchers recommend implementation of experimental studies to verify this efficiency value generated by the splitter blades.
Several studies were used to validate the effect of the geometrical parameters on the efficiency of the PATs. However, the authors of this review did not find a study with the objective of determining the effect of the combination of the impeller rounding parameter (B) with other parameters than impeller diameter (A) and blade inlet angle (I). For this reason, further work could be oriented to determine the best combination of the different geometrical parameters, using impeller rounding as a central parameter, to obtain the lowest cost modification in the rotor. On the other hand, it is necessary to determine the effect of the implementation of the blade guide distributor on the pump in order to correctly orient the flow in both pump and turbine modes. As a first approximation, a CFD technique would be used, as this technique offers great potential for finding the best geometric and operational configuration, thus preventing damage caused by instabilities and establishing potentially critical areas for cavitation damage.
h | head conversion factor | [-] |
q | flow rate conversion factor | [-] |
g | gravity | [m/sec2] |
D1 | inlet diameter | [m] |
D2 | outlet diameter | [m] |
H | head | [m] |
HP | head of the PAT as pump | [m] |
HT | head of the PAT as turbine | [m] |
Hsite | head of the site | [m] |
N | rotational speed | [rpm] |
Ns | specific speed | [rpm m3/4 s-1/2] |
Nsp | specific speed of the PAT as pump | [rpm m3/4 s-1/2] |
Nst | specific speed of the PAT as turbine | [rpm m3/4 s-1/2] |
P | power | [kW] |
Q | flow rate | [m3/s] |
QP | flow rate of the PAT as pump | [m3/s] |
QT | flow rate of the PAT as turbine | [m3/s] |
Qsite | flow rate of the site | [m3/s] |
Greek letters | ||
ρ | density | [kg/m3] |
η | efficiency | [-] |
η | T efficiency of the PAT as turbine at BEP | [-] |
Abbreviations | ||
PAT | Pump as Turbine | |
RES | Renewable Energy Sources | |
IRENA | International Renewable Energy Agency | |
PSH | Pumped-Storage Hydroelectric | |
WF | Wind Farms | |
ALCC | Annual Life Cycle Cost Study | |
CRF | Capital Recovery Factor | |
Ac | Annual expenses | |
EGE | Energy Generation Equipment | |
CW | Civil Work | |
IGC | Induction Generator Controller | |
LCOE | Levelized Cost of Electricity | |
PSPS | Pumped Storage Power Station | |
LCOS | Levelized Cost of Storage | |
CAES | Compressed Air Energy Storage | |
PRV | Pressure Reducing Valves | |
EU | European Union | |
SHP | Small Hydropower Plants | |
MHP | Micro Hydropower Plants | |
BEP | Best Efficiency Point | |
FEM | Finite Element Method | |
CFD | Computational Fluid Dynamics | |
NSPH | Net Positive Suction Head | |
DOE | Design of Experiments | |
YRE | Year round efficiency | |
T | Theoretical | |
N | Numerical | |
E | Experimental | |
A | impeller diameter | |
B | inlet impeller rounding | |
C | number of blades | |
D | splitter blade | |
E | blade wrap angle | |
F | blade profile | |
G | blade thickness | |
H | blade lean | |
I | blade inlet angle |
The Energy Pillars of Society: Perverse Interactions of Human Resource Use, the Economy, and Environmental Degradation ,Biophys. Econ. Resour. Qual , Vol. 3 (1),pp 2 , 2018, https://doi.org/10.1007/s41247-018-0035-6
, Sustainable Entrepreneurship and Corporate Political Activity: Overcoming Market Barriers in the Clean Energy Sector ,Entrep. Theory Pract , Vol. 39 (3),pp 633-654 , 2015, https://doi.org/10.1111/etap.12055
, The irreversible momentum of clean energy ,Science (80-. ) , Vol. 355 (6321),pp 126-129 , 2017, https://doi.org/10.1126/science.aam6284
, A review on clean energy solutions for better sustainability ,Int. J. Energy Res , Vol. 39 (5),pp 585-606 , 2015, https://doi.org/10.1002/er.3329
, - , IRENA, Renewable Power Generation Costs in 2018, 2019
- , REN21, Renewables 2019 Global Status Report, 2019
Energy storage systems-Characteristics and comparisons ,Renew. Sustain. Energy Rev , Vol. 12 (5),pp 1221-1250 , 2008, https://doi.org/10.1016/j.rser.2007.01.023
, Classification and assessment of energy storage systems ,Renew. Sustain. Energy Rev , Vol. 75 ,pp 1187–1197 , 20162017, https://doi.org/10.1016/j.rser.2016.11.102
, Small and Mid-Size Pump-Turbines with Variable Speed ,Energy Power Eng , Vol. 05 (02),pp 48-54 , 2013, https://doi.org/10.4236/epe.2013.52A007
10
, A review of energy storage technologies for wind power applications ,Renew. Sustain. Energy Rev , Vol. 16 (4),pp 2154-2171 , 2012, https://doi.org/10.1016/j.rser.2012.01.029
11
, National Workshop on Pumped Storage Hydropower Projects ,in Basics of the pump storage Technology: technical solutions, possibilities, function in grid and benefits, financial aspects of PSP National Workshop on Pumped Storage Hydropower Projects , (387), 2018
12
, Integration of Renewable Energy Sources in future power systems: The role of storage ,Renew. Energy , Vol. 75 ,pp 14-20 , 2015, https://doi.org/10.1016/j.renene.2014.09.028
13
, Economic evaluation of wind-powered pumped storage system ,Syst. Eng. Procedia , Vol. 4 (2011),pp 107-115 , 2012, https://doi.org/10.1016/j.sepro.2011.11.055
14
, Investment in wind power and pumped storage in a real options model ,Renew. Sustain. Energy Rev , Vol. 16 (4),pp 2242-2248 , 2012, https://doi.org/10.1016/j.rser.2012.01.025
15
, Optimization model for long-distance integrated transmission of wind farms and pumped-storage hydropower plants ,Appl. Energy , Vol. 242 ,pp 285–293 , 2019, https://doi.org/10.1016/j.apenergy.2019.03.080
16
, The features of sustainable Solar Hydroelectric Power Plant ,Renewable Energy , Vol. 34 (7),pp 1742-1751 , 2009, https://doi.org/10.1016/j.renene.2008.12.033
17
, Techno-economic role of PV tracking technology in a hybrid PV-hydroelectric standalone power system ,Appl. Energy , Vol. 212 ,pp 84–108 , 20172018, https://doi.org/https://doi.org/10.1016/j.apenergy.2017.12.030
18
, Modelling and optimisation of a hybrid PV-wind turbine-pumped hydro storage energy system for mini-grid application in coastline communities ,J. Clean. Prod , Vol. 250 (119578), 2019, https://doi.org/10.1016/j.jclepro.2019.119578
19
, Optimal configuration assessments of hybrid renewable power supply for rural healthcare facilities ,Energy Reports , Vol. 2 ,pp 141-146 , 2016, https://doi.org/10.1016/j.egyr.2016.06.001
20
, Solar and wind power generation systems with pumped hydro storage: Review and future perspectives ,Renew. Energy , Vol. 148 ,pp 176-192 , 2020, https://doi.org/10.1016/j.renene.2019.11.157
21
, A stand-alone photovoltaic power system for remote villages using pumped water energy storage ,Energy , Vol. 29 (1),pp 57-69 , 2004, https://doi.org/10.1016/j.energy.2003.08.008
22
, Large-scale integration of renewable energies and impact on storage demand in a European renewable power system of 2050-Sensitivity study ,J. Energy Storage , Vol. 6 ,pp 1-10 , 2016, https://doi.org/10.1016/j.est.2016.02.004
23
, Review of energy storage system for wind power integration support ,Appl. Energy , Vol. 137 ,pp 545-553 , 2015, https://doi.org/10.1016/j.apenergy.2014.04.103
24
, Increasing the Flexibility of Combined Heat and Power Plants With Heat Pumps and Thermal Energy Storage ,J. Energy Resour. Technol , Vol. 140 (2),pp 020907 , 2017, https://doi.org/10.1115/1.4038461
25
, Cost analysis of pump as turbine for pico hydropower plants - A case Study ,Procedia Engineering , Vol. 51 ,pp 721-726 , 2013, https://doi.org/10.1016/j.proeng.2013.01.103
26
, Pump as turbine - A pico-hydro alternative in Lao People’s Democratic Republic ,Renew. Energy , Vol. 35 (5),pp 1109-1115 , 2010, https://doi.org/10.1016/j.renene.2009.08.022
27
, PAT System Economic Analysis ,Pumps as Turbines Fundamentals and applications ,pp 173–178 , 2018
28
, Analysis of emerging technologies in the hydropower sector ,Renew. Sustain. Energy Rev , Vol. 113 (109257), 2019, https://doi.org/10.1016/j.rser.2019.109257
29
, Pumped storage power plants ,Renew. Energy ,pp 165-196 , 2006, https://doi.org/10.1007/10858992_7
30
, Status of pumped hydro-storage schemes and its future in India ,Renew. Sustain. Energy Rev , Vol. 19 ,pp 208-213 , 2013, https://doi.org/10.1016/j.rser.2012.11.001
31
, Comparison of electricity storage options using levelized cost of storage (LCOS) method ,Appl. Energy , Vol. 183 ,pp 1594-1606 , 2016, https://doi.org/10.1016/j.apenergy.2016.08.165
32
, Study of a Pump as Turbine for a Hydraulic Urban Network Using a Tridimensional CFD Modeling Methodology ,Energy Procedia , Vol. 82 ,pp 201-208 , 2015, https://doi.org/10.1016/j.egypro.2015.12.020
33
, Pump as turbine (PAT) design in water distribution network by system effectiveness ,Water (Switzerland) , Vol. 5 (3),pp 1211-1225 , 2013, https://doi.org/10.3390/w5031211
34
, Performance of vertical-axis pumps as turbines ,J. Hydraul. Res , Vol. 56 (4),pp 482-493 , 2018, https://doi.org/10.1080/00221686.2017.1399932
35
, Experimental study of viscosity effects on a pump as turbine performance ,Renew. Energy , Vol. 127 ,pp 539-547 , 2018, https://doi.org/10.1016/j.renene.2018.04.084
36
, Pumps as turbines for efficient energy recovery in water supply networks ,Renew. Energy , Vol. 122 ,pp 17-25 , 2018, https://doi.org/10.1016/j.renene.2018.01.053
37
, - 38 , Pumping Electrical Plant, Control and Instrumentation, Twort’s Water Supply, 2017
Reverse running pumps analytical, experimental and computational study: A review ,Renew. Sustain. Energy Rev , Vol. 14 (7),pp 2059-2067 , 2010, https://doi.org/10.1016/j.rser.2010.04.006
39
, Pumps as turbines for water industry ,World Pumps , Vol. 2009 (8),pp 22-23 , 2009, https://doi.org/10.1016/S0262-1762(09)70283-4
40
, - 41 , , Turbomáquinas hidráulicas : turbinas hidráulicas, bombas, ventiladores, 2009
- 42 , Manual on pumps used as turbines, MHPG. gate, 1992
A technical discussion on microhydropower technology and its turbines ,Renew. Sustain. Energy Rev , Vol. 35 ,pp 445-459 , 2014, https://doi.org/10.1016/j.rser.2014.04.035
43
, Using a statistical-numerical procedure for the selection of pumps running as turbines to be applied in water pipelines: Study cases ,J. Sustain. Dev. Energy, Water Environ. Syst , Vol. 6 (2),pp 323-340 , 2018, https://doi.org/10.13044/j.sdewes.d5.0181
44
, Technical and economic analysis of Pumps-as-Turbines (PaTs) used in an Italian Water Distribution Network (WDN) for electrical energy production ,Energy Procedia , Vol. 158 ,pp 117-122 , 2019, https://doi.org/10.1016/j.egypro.2019.01.055
45
, Experimental investigation and performance prediction modeling of a single stage centrifugal pump operating as turbine ,Energy Procedia , Vol. 126 ,pp 589-596 , 2017, https://doi.org/10.1016/j.egypro.2017.08.218
46
, Performance of centrifugal pumps running in reverse as turbine: Part Ⅱ- systematic specific speed and specific diameter based performance prediction ,Renew. Energy , Vol. 99 ,pp 188-197 , 2016, https://doi.org/10.1016/j.renene.2016.06.052
47
, Theoretical, numerical and experimental prediction of pump as turbine performance ,Renew. Energy , Vol. 48 ,pp 507-513 , 2012, https://doi.org/10.1016/j.renene.2012.06.002
48
, An optimization routine on a prediction and selection model for the turbine operation of centrifugal pumps ,Exp. Therm. Fluid Sci , Vol. 34 (2),pp 152-164 , 2010, https://doi.org/10.1016/j.expthermflusci.2009.10.004
49
, Experimental study of characteristic curves of centrifugal pumps working as turbines in different specific speeds ,Exp. Therm. Fluid Sci , Vol. 32 (3),pp 800-807 , 2008, https://doi.org/10.1016/j.expthermflusci.2007.10.004
50
, , Centrifugal and axial flow pumps: theory design and applicationJohn Wiley , 1957
51
, Convert pumps to turbines and recover HP ,Hydrocarb. Process. Pet. Refin , Vol. 41 (10),pp 173–174 , 1962
52
, Centrifugal pump or water turbine ,Pipe Line News ,pp 25–27 , 1963
53
, Conversion of pumps to turbines ,GSA Inter corp., Katonah, New York , 1980
54
, Small hydroelectric project-use of centrifugal pumps as turbines ,Kirloskar Electr. Co., Bangalore, India , 1985
55
, Pumpen als Turbinen fur Kleinkraftwerke ,Wasserwirtschaft , Vol. 77 (10),pp 531–537 , 1987
56
, Serien-Kreiselpumpen im Turbinenbetrieb ,Pumpentagung Karlsruhe, Ger , 1988
57
, - 58 , Cost minimisation in micro-hydro systems using pumps-as-turbines, 1994
Pumps as turbines (PAT) for small hydro ,INDIAN J. POWER RIVER Val. Dev , Vol. 49 ,pp 44–48 , 1999
59
, Experimental Investigation of Centrifugal Pump Working as Turbine for Small Hydropower Systems ,ENERGY Sci. Technol , Vol. 1 (1),pp 79–86 , 2011
60
, Experimental activity at test rig validating correlations to select pumps running as turbines in microhydro plants ,Energy Convers. Manag , Vol. 149 ,pp 781-797 , 2017, https://doi.org/10.1016/j.enconman.2017.03.013
61
, Pressure fluctuations in the vaneless space of High-head pump-turbines—A review ,Renew. Sustain. Energy Rev , Vol. 41 ,pp 965-974 , 2014, https://doi.org/10.1016/j.rser.2014.09.011
62
, Failure investigation of a large pump-turbine runner ,Eng. Fail. Anal , Vol. 23 ,pp 27-34 , 2012, https://doi.org/10.1016/j.engfailanal.2012.01.012
63
, Analysis of the dynamic response of pump-turbine impellers. Influence of the rotor ,Mech. Syst. Signal Process , Vol. 68–69 ,pp 330–341 , 2016, https://doi.org/10.1016/j.ymssp.2015.05.034
64
, S-shaped characteristics on the performance curves of pump-turbines in turbine mode – A review ,Renew. Sustain. Energy Rev , Vol. 60 ,pp 836-851 , 2016, https://doi.org/10.1016/j.rser.2015.12.312
65
, - , Hydraulic turbines, storage pumps and pump-turbines, 1999 66
Analysis of S Characteristics and Pressure Pulsations in a Pump-Turbine With Misaligned Guide Vanes ,J. Fluids Eng , Vol. 135 (5),pp 511011-511016 , 2013, https://doi.org/10.1115/1.4023647
67
, Numerical simulation on the S characteristics and pressure fluctuation of reduced pump-turbine at start-up condition ,IOP Conference Series: Earth and Environmental Science , Vol. 15 (062034),pp 7 , 2012, https://doi.org/10.1088/1755-1315/15/6/062034
68
, Stability Limits of Reversible-Pump Turbines in Turbine Mode of Operation and Measurements of Unstable Characteristics ,J. Fluids Eng , Vol. 134 (11111202), 2012, https://doi.org/10.1115/1.4007589
69
, Unsteady simulation and analysis for hump characteristics of a pump turbine model ,Renew. Energy , 2015, https://doi.org/10.1016/j.renene.2014.12.004
70
, Experimental investigation of a pump-turbine at off-design operating conditions ,International meeting of the workgoup on cavitation and dynamic problems in hidraulic machinary and systems ,pp 339–348 , 2009
71
, - 72 , CFD for centrifugal pumps: A review of the state-of-the-art, Procedia Eng, 20122013
Predicting the Inception Cavitation of a Reversible Pump- Turbine in Pump Mode ,J. Phys. Conf. Ser , Vol. 656 (1),pp 7-11 , 2015, https://doi.org/10.1088/1742-6596/656/1/012077
73
, Cavitation behavior study in the pump mode of a reversible pump-turbine ,Renew. Energy , Vol. 125 ,pp 655-667 , 2018, https://doi.org/10.1016/j.renene.2018.02.114
74
, High head pump-turbine : Pumping mode numerical simulations with a cavitation model for off-design conditions ,IOP Conf. Ser. Earth Environ. Sci , Vol. 22 (1),pp 1-11 , 2014, https://doi.org/10.1088/1755-1315/22/3/032048
75
, Numerical investigation of the hump characteristic of a pump-turbine based on an improved cavitation model ,Comput. Fluids , Vol. 68 ,pp 105-111 , 2012, https://doi.org/10.1016/j.compfluid.2012.08.001
76
, Design and performance evaluation of a pump-as-turbine micro-hydro test facility with incorporated inlet flow control ,Renew. Energy , 2015, https://doi.org/10.1016/j.renene.2014.12.027
77
, Dynamic response and governor tuning of a long penstock pumped-storage hydropower plant equipped with a pump-turbine and a doubly fed induction generator ,Energy Convers. Manag , Vol. 106 ,pp 151-164 , 2015, https://doi.org/10.1016/j.enconman.2015.09.030
78
, The influence of changing hydropower potential on performance parameters of pumps in turbine mode ,Energies , Vol. 12 (11), 2019, https://doi.org/10.3390/en12112103
79
, A Performance Prediction Method for Pumps as Turbines (PAT) Using a Computational Fluid Dynamics (CFD) Modeling Approach ,Energies , Vol. 10 (1), 2017, https://doi.org/10.3390/en10010103
80
, Experimental Design and Analysis of Pump as Turbine for Microhydro System ,IOP Conf. Ser. Mater. Sci. Eng , Vol. 217 (012014), 2017, https://doi.org/10.1088/1757-899X/217/1/012014
81
, Optimization design of a reversible pump–turbine runner with high efficiency and stability ,Renew. Energy , Vol. 81 ,pp 366-376 , 2015, https://doi.org/10.1016/j.renene.2015.03.050
82
, Effects of impeller trimming influencing pump as turbine ,Comput. Fluids , Vol. 67 ,pp 72-78 , 2012, https://doi.org/10.1016/j.compfluid.2012.07.009
83
, Effects of impeller diameter and rotational speed on performance of pump running in turbine mode ,Energy Convers. Manag , Vol. 89 ,pp 808-824 , 2015, https://doi.org/10.1016/j.enconman.2014.10.036
84
, Determination of special impeller diameter for pump as turbine and its effects on turbine performance ,Trans. Chinese Soc. Agric. Eng , Vol. 32 (15),pp 60-67 , 2016, https://doi.org/10.11975/j.issn.1002-6819.2016.15.009
85
, Internal hydraulic analysis of impeller rounding in centrifugal pumps as turbines ,Exp. Therm. Fluid Sci , Vol. 35 (1),pp 121-134 , 2011, https://doi.org/10.1016/j.expthermflusci.2010.08.013
86
, CFD Modelling of a Pump as Turbine (PAT) with Rounded Leading Edge Impellers for Micro Hydro Systems ,MATEC Web Conf , Vol. 87 , 2017, https://doi.org/10.1051/matecconf/20178705004
87
, Inlet impeller rounding in pumps as turbines: An experimental study to investigate the relative effects of blade and shroud rounding ,Exp. Therm. Fluid Sci , Vol. 82 ,pp 333-348 , 2017, https://doi.org/10.1016/j.expthermflusci.2016.11.024
88
, Effects of splitter blade number on the performance of a pump when used as turbine using CFD ,Int. Agric. Eng. J , Vol. 21 (1),pp 1-6 , 2012, https://doi.org/10.1115/1.4007810
89
, CFD Modelling of pump as turbine with various number of blade for microhydro system ,J. Appl. Sci. Process Eng , Vol. 3 (1),pp 17–23 , 2016
90
, Numerical research on effects of splitter blades to the influence of pump as turbine ,Int. J. Rotating Mach , Vol. 2012 , 2012, https://doi.org/10.1155/2012/123093
91
, Numerical Simulation and Orthogonal Design Method Research Effect of Splitter Blade’s Main Geometry Factors on the Performance of Pump as Turbine ,Appl. Mech. Mater , Vol. 456 ,pp 100-105 , 2013, https://doi.org/10.4028/www.scientific.net/AMM.456.100
92
, Effects of Blade Wrap Angle Influencing a Pump as Turbine ,J. Fluids Eng , Vol. 134 (6061102), 2012, https://doi.org/10.1115/1.4006677
93
, Effect of blade wrap angle in hydraulic turbine with forward-curved blades ,Int. J. Hydrogen Energy , Vol. 42 (29),pp 18709-18717 , 2017, https://doi.org/10.1016/j.ijhydene.2017.04.185
94
, Study on the impact of blades wrap angle on the performance of pumps as turbines used in water supply system of high-rise buildings ,Int. J. Low-Carbon Technol , Vol. 13 (1),pp 102-108 , 2018, https://doi.org/10.1093/ijlct/cty002
95
, Blade profile optimization of pump as turbine ,Adv. Mech. Eng , Vol. 7 (9),pp 1-9 , 2015, https://doi.org/10.1177/1687814015605748
96
, Research on blade thickness influencing pump as turbine ,Adv. Mech. Eng , Vol. 2014 ,pp 1-8 , 2014, https://doi.org/10.1155/2014/190530
97
, Noise reduction in centrifugal pump as turbine: Influence of leaning blade or tongue ,J. Vibroengineering , Vol. 18 (4),pp 2667-2682 , 2016, https://doi.org/10.21595/jve.2016.16811
98
, Performance of two types of hydraulic turbine impellers ,J. Cent. South Univ. (Science Technol , Vol. 48 (4),pp 977-983 , 2017, https://doi.org/10.11817/j.issn.1672−7207.2017.04.017
99
, Numerical simulation and validation of effects of blade inlet angle on performance of pump-as-turbine ,Trans. Chinese Soc. Agric. Eng , Vol. 33 (15),pp 98-104 , 2017, https://doi.org/10.11975/j.issn.1002-6819.2017.15.012
100
, The method for determining blade inlet angle of special impeller using in turbine mode of centrifugal pump as turbine ,Renew. Energy , Vol. 109 ,pp 518-528 , 2017, https://doi.org/10.1016/j.renene.2017.03.054
101
, Theoretical, experimental, and numerical study of special impeller used in turbine mode of centrifugal pump as turbine ,Energy , Vol. 130 ,pp 473-485 , 2017, https://doi.org/10.1016/j.energy.2017.04.156
,